What is a Robotic Arm End Effector?
In the world of robotics, the end effector plays a key role in enabling machines to interact with the physical environment. Whether it’s picking up an object, performing precision welding, or assembling components, the end effector is the functional “hand” of the robotic arm. It is also referred to as end of arm tooling (EOAT). Let’s dive into the history of end effectors, explore industry-relevant examples, and provide technical details about their construction and applications.
An end effector is a device or tool that is attached to the end of a robotic arm to enable it to perform a specific task. Its function varies based on the requirements of the task it needs to execute, from gripping, welding, and cutting to painting, polishing, or even surgery. It is the point of interaction between the robot and the objects in its workspace, making it a critical component in robotic automation.
A Brief History of Robotic End Effectors
The development of end effectors can be traced back to the mid-20th century, alongside the evolution of industrial robots. Early robotic arms, such as the Unimate, which made its debut in 1961 in a General Motors assembly line, were equipped with simple grippers. These rudimentary end effectors had limited capabilities but were a massive step forward in industrial automation.
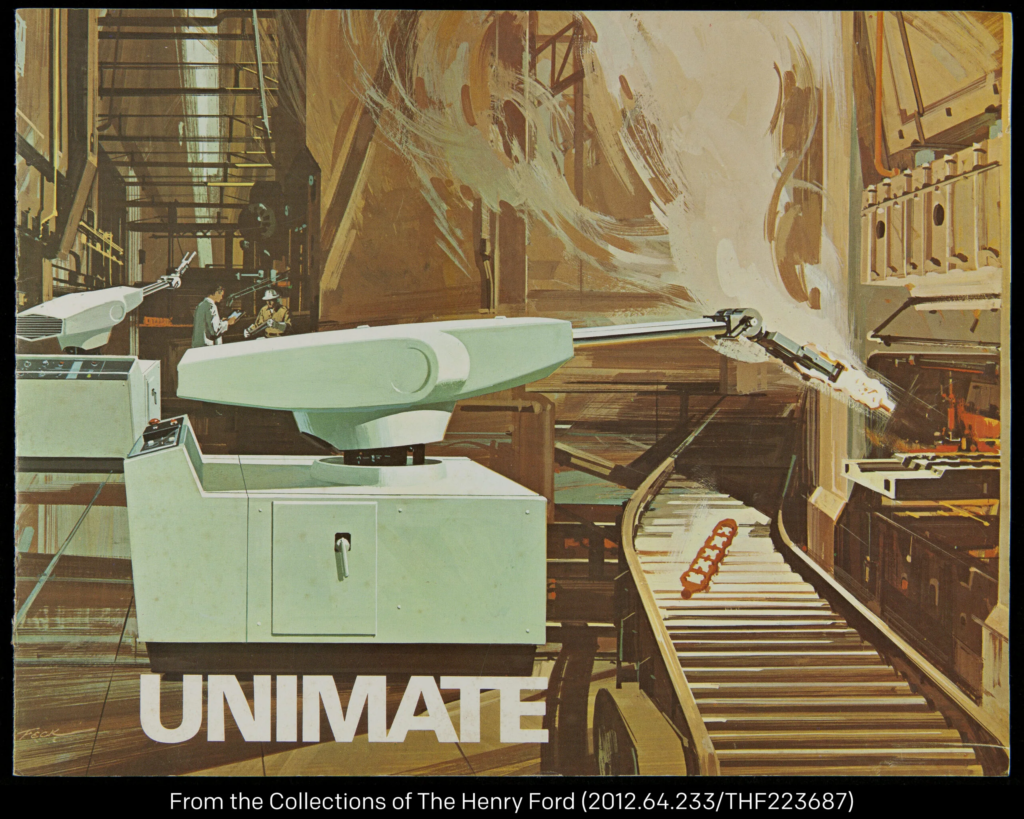
As industries began to demand more complex tasks from robotic systems, the need for sophisticated end effectors grew. By the 1980s, advancements in robotic technology enabled the development of specialized end effectors capable of performing delicate and intricate tasks, such as spot welding in the automotive industry or precision pick-and-place operations in electronics manufacturing.
In the 21st century, end effectors became even more advanced, benefiting from developments in sensor technology, materials science, and machine learning. Modern end effectors can be equipped with force sensors, tactile feedback systems, and adaptive gripping technologies to handle a broader range of tasks with improved accuracy and reliability.
Types of Robotic End Effectors
Today, the design and selection of an end effector are determined by the task at hand. There are several primary categories of robotic end effectors.
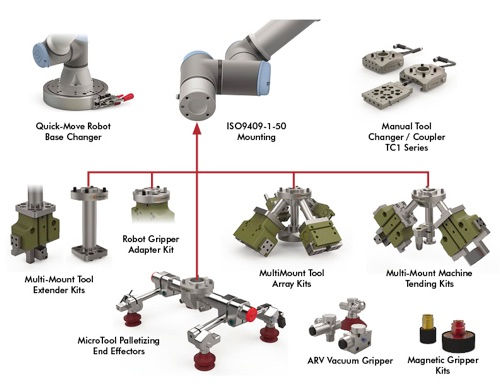
- Grippers:
- Mechanical grippers: Use jaws or fingers to grab and release objects. These are the most common end effectors, found in applications ranging from packaging to materials handling.
- Vacuum grippers: Use suction to lift flat or porous objects, frequently seen in packaging, electronics, and logistics industries.
- Magnetic grippers: Ideal for handling ferromagnetic materials such as steel sheets and parts.
- Example: Schunk PGN-plus-E, a mechatronic universal gripper widely used in assembly and pick-and-place applications.
- Welding Torches:
- Designed to perform various welding tasks like MIG, TIG, and spot welding. These end effectors are common in the automotive industry for joining metal parts.
- Example: Lincoln Electric’s Smart Welding Arm, which combines vision systems with robotic arms to deliver precision welding.
- Material Removal Tools:
- These include tools for cutting, drilling, grinding, and deburring. They are used in industries like aerospace and automotive where precision and speed are crucial.
- Example: ATI’s Industrial Robotic Deburring Tools, designed for accurate material removal on various surfaces.
- Paint Sprayers:
- Specialized end effectors for the uniform application of paint or coating materials. Often used in the automotive and furniture manufacturing industries.
- Sensor-Based End Effectors:
- These are adaptive systems that incorporate sensors for real-time feedback, such as force-torque sensors for assembly tasks that require a delicate touch or vision-based systems for precision alignment.
- Example: OnRobot’s RG2 Gripper, which can adapt its grip based on the object’s shape and size.
Industry Applications of Robotic End Effectors
Automotive Manufacturing
The automotive sector was one of the earliest adopters of robotic automation, and welding end effectors were crucial to this transformation. Modern end effectors in automotive production lines not only perform spot and arc welding but also handle material handling, inspection, and assembly tasks. For example, ABB’s IRB 6700 equipped with welding end effectors is widely used in vehicle manufacturing plants to ensure precise, high-quality welds.
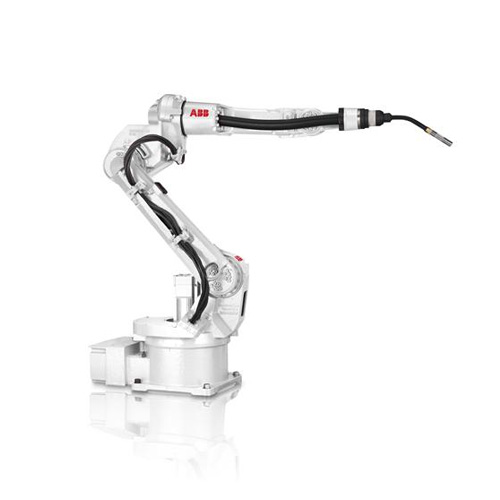
Electronics Manufacturing
In electronics, robotic arms equipped with vacuum grippers and precision manipulators are used for assembling small, delicate components such as circuit boards and chips. The ability to handle tiny parts without causing damage is critical in this field. Fanuc robots, equipped with vacuum-based end effectors, are a common sight in electronics manufacturing.
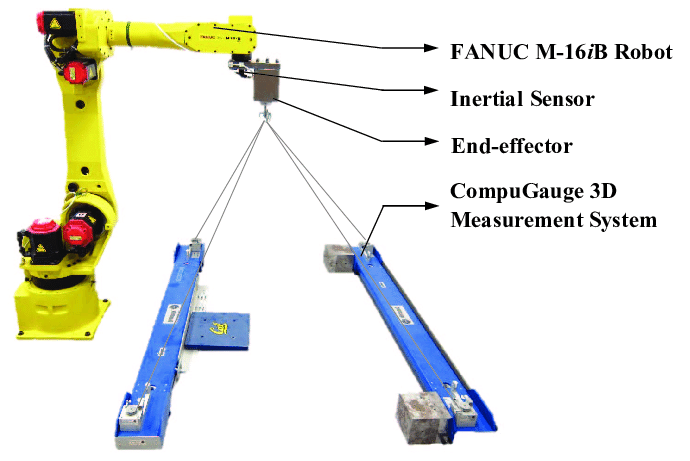
Food and Beverage Industry
Robotic arms with soft grippers or vacuum systems are extensively used in food packaging and processing. These end effectors must meet stringent hygiene standards while being gentle enough to handle perishable goods without damage. Schmalz range of soft grippers are particularly suitable for handling food products like fruits, meats, and bakery items.

Aerospace Industry
In aerospace, end effectors are required for tasks like drilling and riveting, often in confined spaces with demanding accuracy requirements. For instance, KUKA robotic arms equipped with drilling end effectors are used to precisely create thousands of holes in aircraft fuselages, ensuring structural integrity and efficiency.
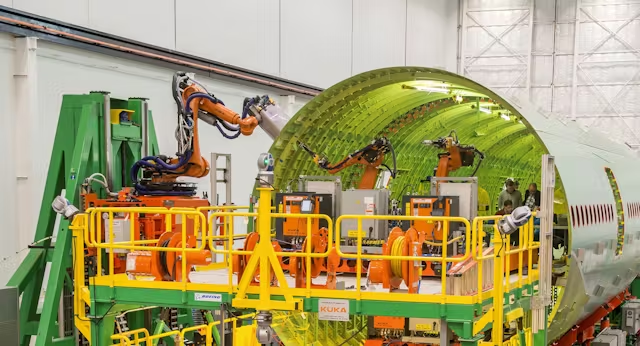
Some Specs of Robotic End Effectors
End effectors are designed to integrate seamlessly with the robotic arm. These specifications influence end efffector design and performance.
- Payload Capacity: The weight that an end effector can handle without compromising performance. For example, a vacuum gripper designed for large glass panels must handle high payloads, while a precision gripper for electronics may handle only a few grams.
- Grip Force and Tolerance: Mechanical grippers are rated by their grip force, which determines how firmly they can hold an object. Tolerances for handling fragile items are also considered in industries such as electronics or food processing.
- Material Construction: Depending on the environment (e.g., cleanrooms, high-temperature areas), end effectors may be constructed from specialized materials like stainless steel, aluminum, or even biocompatible plastics.
- Communication and Control: Modern end effectors often incorporate sensors and feedback loops that allow them to adjust their operations in real time. EtherCAT, Profinet, and other industrial communication protocols enable seamless integration with the broader robotic system.
The Future of Robotic End Effectors
The future of end effectors lies in increased intelligence, adaptability, and customization. Emerging trends include:
- Soft robotics for handling complex, irregular shapes.
- Self-calibrating systems that adjust to changes in the environment in real time.
- AI-powered vision systems that enable robots to “see” and “decide” on the best way to grasp objects.
As industries continue to embrace automation, the role of robotic end effectors will expand, driving greater efficiency, precision, and flexibility across sectors.

Robotic end effectors have come a long way from simple mechanical grippers to sophisticated multi-functional tools capable of tackling complex tasks across industries. As technology evolves, so too will these critical components, offering new possibilities in automation and transforming how industries operate. Whether in automotive production, electronics assembly, or food processing, end effectors continue to be at the forefront of industrial innovation.

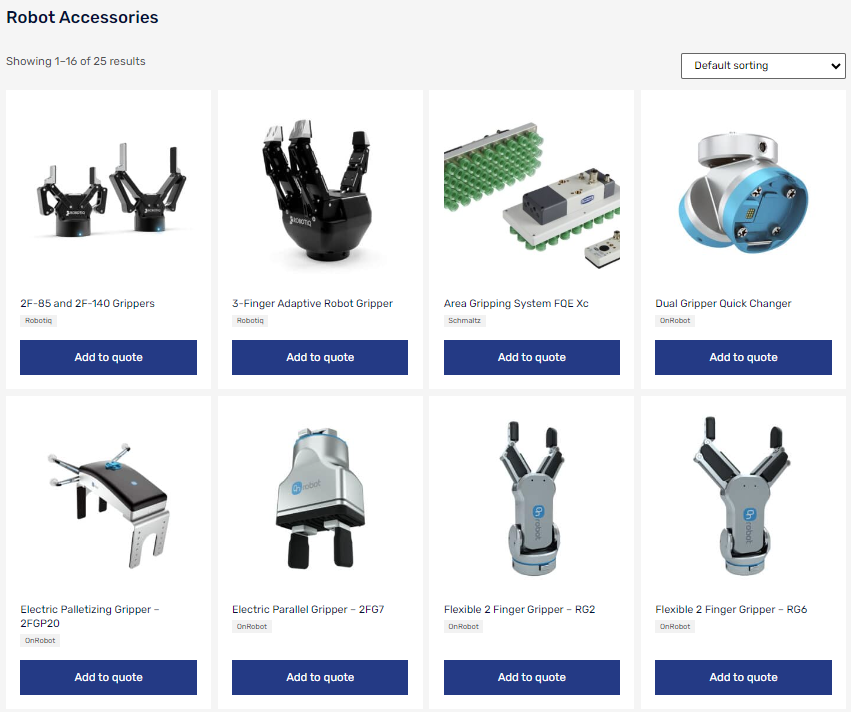
Go to Browse on the industrial-robotics.com.au webpage to check out our range of Robot Accessories and get the perfect end effector for your project.
Can’t find what you are looking for? No problem! Contact the Industrial Robotics team at either 1300476258 or email sales@industrial-robotics.com.au – our friendly staff are happy to quote you the right product for the job.